Integrierte Planung und effizienter Betrieb für klimaschonende Bauchemie
R&I, Fluidplanung und Elektrik integriert
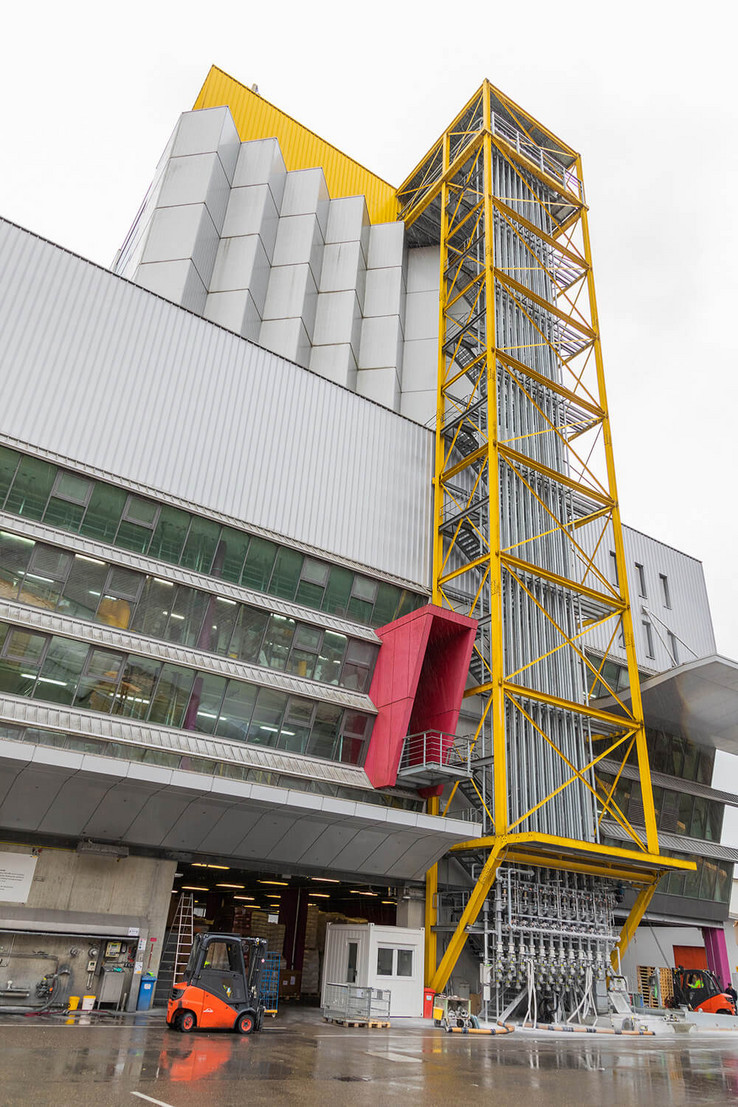
Die Produktionsanlage von Sto in Stühlingen mit Blick auf die Rohstoffannahme und den Siloturm.
© Sto
Der Immobiliensektor boomt – und davon profitieren nicht nur Baugewerbe und Handwerk, sondern auch die Bauchemie. Mit Farben und Lacken, Systemen für Beschichtung und Wärmedämmung bietet das Traditionsunternehmen Sto, was die Branche dringend benötigt. Die wachsende Nachfrage brachte die Produktion am Stammsitz in Baden-Württemberg jedoch an ihre Grenzen. Für das Retrofit einer Produktionsanlage entschied sich Sto für Engineering-Lösungen von EPLAN – und spart so die Hälfte der Zeit, die für Instandhaltung und regelmäßige verfahrenstechnische Anpassungen bislang nötig war.
Stühlingen ist gelb-gepunktet. Ob im Garten, auf dem Balkon oder in der Garage – wer durch die baden-württembergische Kleinstadt spaziert, sieht ständig irgendwo einen leuchtend gelben Eimer, zweckentfremdet für Haushalt und Gartenarbeit. Der Grund prangt in Form von drei schwarzen Lettern kontrastreich auf den 15-Liter-Gefäßen: Stühlingen ist der Hauptsitz von Sto. Aus einem Kalkwerk von der namensgebenden Familie Stotmeister gegründet, ist der Hersteller heute für seine Farben, Putze, Lacke, Beschichtungs- und Wärmedämm-Verbundsysteme weltweit bekannt. Um die Auswirkungen der Produkte auf Umwelt und Klima weiter zu verbessern, betreibt Sto viel Forschung und Entwicklung. Ziele sind dabei neben leicht recycelbaren Dämmsystemen und nachhaltigen Rohstoffen auch eine sichere, möglichst energie- und ressourceneffiziente Produktion.
Auf der Suche nach mehr Flexibilität und Leistungsfähigkeit
Im Fokus der jüngsten Bemühungen von Sto, die Produktion gleichzeitig effizienter und leistungsfähiger zu machen, stand die „Produktion 3“: die Leistungsanlage, die am Standort Stühlingen die größten Tonnagen zum Gesamtdurchsatz beiträgt. 1980 errichtet, wurde die Anlage schon zehn Jahre später zum ersten Mal einem Retrofit unterzogen, eine für die 1990er Jahre zeitgemäße Prozessautomatisierung hielt Einzug in die Produktion. „Das hat über lange Zeit hinweg hervorragend funktioniert“, erinnert sich Joachim Hauschel, der bei Sto für die Planung und Automatisierung der Anlagen in Stühlingen mit EPLAN verantwortlich ist.
Im Laufe der Jahre häuften sich jedoch die Probleme: Die Beschaffung von Ersatzteilen für Komponenten der Mess-, Steuer- und Regeltechnik (MSR) wurde immer schwieriger, und auch das wachsende Produktportfolio stellte die Herstellung vor Herausforderungen. „Denn unsere Anlagen entwickeln sich kontinuierlich weiter“, erklärt Hauschel: „Immer, wenn im Labor ein neues Produkt entwickelt und zur Marktreife gebracht wird, müssen wir beispielsweise Platz im Tanklager für neue Rohstoffe schaffen, Kapazitäten erhöhen oder neue Rohrleitungen verlegen.“ Das immer umfangreichere verfahrenstechnische Engineering brachte auch die in die Jahre gekommene Prozesssteuerung irgendwann an ihre Grenzen, erklärt Hauschel: „Wir hatten schlicht keine Schnittstellen mehr frei, es war alles belegt.“
2019 war eine umfassende Erweiterung schließlich unumgänglich, um die Kapazität der Produktion und auch der Automatisierung auf den neuesten Stand zu bringen. In diesem Rahmen wollten Hauschel und seine Kollegen aus dem Planungs- und Automatisierungsteam noch ein weiteres Hemmnis beseitigen: „Die bestehende Elektrokonstruktion der Anlage hatten wir bereits digital mit EPLAN projektiert. Doch das gesamte Rohrleitungs- und Instrumentenfließschema existierte lediglich auf Papier oder in Excel-Tabellen – und das auch nur sehr spärlich, weil bei Änderungen nie nachgepflegt wurde.“
Die Folgen bekam das Anlagenpersonal regelmäßig zu spüren, wenn Instandhaltungsmaßnahmen oder Verfahrensanpassungen anstanden: Oft mussten betroffene Rohrleitungen bei Anlagenbegehungen vor Ort nachverfolgt werden. „Manche Leitungen bin ich fünfmal abgelaufen – mit fünf verschiedenen Ergebnissen. Irgendeine Abzweigung kann man schließlich immer übersehen“, erinnert sich Hauschel an die mühsame Arbeit.
Eine integrierte Plattform als zentrale Datenbasis
Um eine stets verlässliche Datenbasis zu erhalten, dem eigenen Personal die Arbeit zu erleichtern und auch dem mit dem Retrofit betrauten Steuerungsbauer ein vollständiges Bild des Ist- und Sollzustands der Produktion zu liefern, schrieb Hauschel deshalb zusätzlich zur Elektrokonstruktion auch das vollständig digitale Rohrleitungs- und Instrumentenfließschema (R&I) ins Pflichtenheft. „Dafür suchten wir eine einheitliche Plattform, die uns alles aus einer Hand bietet“, erklärt Hauschel. Eine Suche, die schnell zum Ziel führte: Die EPLAN Plattform bietet die zeitgemäße technische Basis für modernes Engineering, das die Digitalisierung aller Bereiche der Industrie ermöglicht. EPLAN Electric P8 ist die Best-in-Class-Lösung für das Erzeugen von Schalt- und Stromlaufplänen, die detaillierte Auswertungen als integralen Bestandteil der Projektdokumentation automatisch erstellt. Mit EPLAN Preplanning werden Engineering-Daten über alle Planungsphasen hinweg digital gesammelt – von der Elektrotechnik über Fluidtechnik und R&I bis hin zur elektrischen MSR-Technik – und so aufbereitet, dass sie auch für Betrieb und Instandhaltung genutzt werden können.
„Preplanning war uns zwar ein Begriff, aber die Funktionen und Leistungen des Systems kannten wir nicht“, erinnert sich Hauschel. Bei der Besichtigung einer Referenzanlage lernten die Verantwortlichen bei Sto das Werkzeug näher kennen. Den letztlichen Ausschlag gab jedoch ein Dienstleister, den Hauschel schon aus früheren Projekten und Workshops kannte: Kaltschmid Industrial Engineering setzt bei der Elektroplanung und allen weiteren Engineeringprozessen ganz auf EPLAN. „In Gesprächen über unsere Pläne für das Retrofit mit Geschäftsführer Ronny Kaltschmid erkannte ich schnell sein umfassendes Fachwissen über sämtliche EPLAN Tools“, sagt Hauschel. Für die gemeinsame Erstellung der verfahrenstechnischen Pläne zur Anlagenerneuerung in Preplanning erwies sich Kaltschmid somit als perfektes Bindeglied.
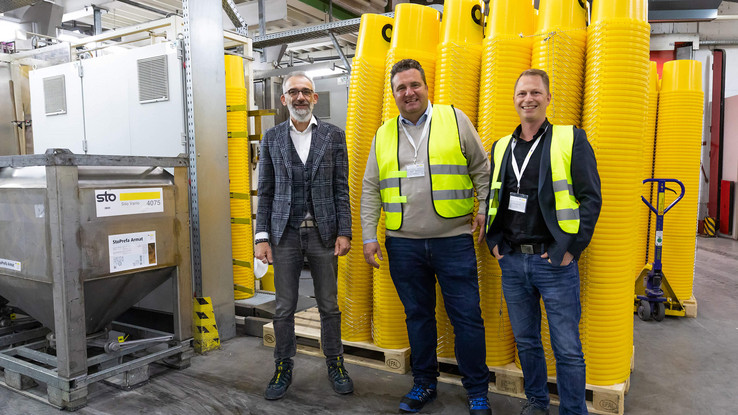
Joachim Hauschel (Sto), Klaus Lechtenbörger (EPLAN) und Ronny Kaltschmid (Kaltschmid Industrial Engineering – v.l.) freuen sich, dass die Anlage in Stühlingen die charismatischen gelben Sto-Eimer dank der Engineering-Lösungen von EPLAN noch effizienter befüllt.
© Sto
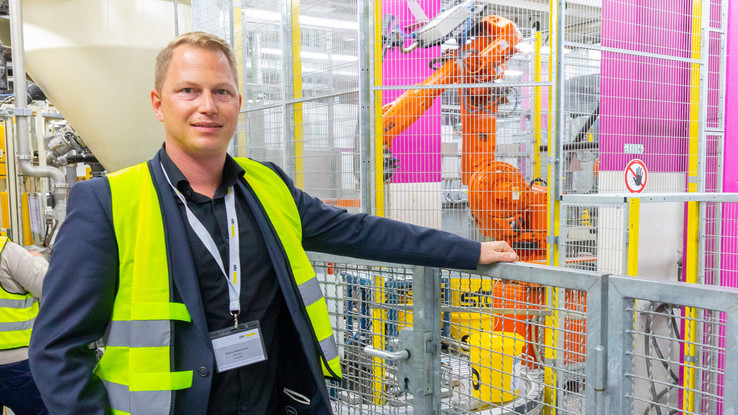
Ronny Kaltschmid (Kaltschmid Industrial Engineering)
© Sto
Integrierte Projektierung und Dokumentation der Pneumatik
„Mit Preplanning können Daten aus dem Engineering schon in der Vorplanung erfasst werden – eine Leistung, die sich für das Projekt mit Sto als ideal erwiesen hat“, beschreibt Kaltschmid die Vorteile des Systems. Die integrierte Funktionsweise half auch, den engen Zeitrahmen einzuhalten, den es beim Umbau zu berücksichtigen galt. „Wir wussten ja, dass wir bis Jahresende 2018 fertig sein mussten, damit der Steuerungsbauer mit seiner Arbeit beginnen kann“, erklärt Hauschel.
Trotz Zeitmangels empfahl Kaltschmid, als dritte Disziplin im Rahmen des Retrofits auch die Fluidtechnik in die integrierte digitale Planung und Projektierung aufzunehmen. Denn alle Absperrklappen in der Produktion von Sto werden von pneumatischen Aktoren gesteuert. „Eine elektrotechnische Planung, die auch die Fluidplanung in die Dokumentation mit einbezieht, vereinfacht die Abläufe im Engineering ebenso wie im Produktionsalltag enorm“, weiß Kaltschmid. Dieser Auffassung schloss Hauschel sich an, sodass im Rahmen des Retrofits nicht nur Elektrotechnik und R&I, sondern auch die Fluidtechnik mit Hilfe von EPLAN Fluid abgebildet wurden.
Aktuelle Dokumentation sichert hohe Anlagenverfügbarkeit
Nach neun Monaten Planung und drei Monaten Bauzeit ging die erneuerte Anlage im Januar 2020 in den Regelbetrieb über. „Schon während der Planungsphase haben wir Maßnahmen durchgeführt, um einen schnellen Wechsel auf die neue Produktionsteuerung sicherzustellen, denn dafür standen uns nur zwei Wochen zur Verfügung“, beschreibt Hauschel den engen Zeitplan. Bedingt durch Just-in-time-Produktion muss das Team der Anlagentechnik zu jeder Zeit eine Anlagenverfügbarkeit von 98,5 Prozent garantieren. Die Spezialisten bei Sto stellen deshalb rund um die Uhr eine Rufbereitschaft sicher. Gibt es ein Problem in einem Anlagenteil, muss einer der Mitarbeiter innerhalb von 30 Minuten vor Ort sein, um sich darum zu kümmern, dass die Produktion so schnell wie möglich wieder fortgesetzt werden kann.
„Genau deshalb ist es unsere unabdingbare Vorgabe, dass wir über eine Dokumentation verfügen, die zu jeder Zeit aktuell ist“, erklärt Hauschel. Praktisch bedeutet die Vorgabe im Extremfall, dass auch und gerade bei einem Einsatz um 3 Uhr nachts im Plan eindeutig ersichtlich sein muss, wo welche Komponenten installiert und wie sie verbunden sind. „EPLAN erfüllt diese Anforderung problemlos“, freut sich Hauschel. So helfen die Tools, Projekte zu visualisieren und verständlicher zu machen. „Einer der größten Vorteile dieses Dreigestirns aus EPLAN Preplanning, Electric P8 und Fluid ist für uns aber, dass wir alle Pläne und Änderungen jetzt auch selbst durchführen können“, resümiert Hauschel nach dem abgeschlossenen Umbau.
Die Mitarbeiter zur selbstständigen Arbeit zu befähigen ist ein Faktor, der den Planungs- und Automatisierungsverantwortlichen im betrieblichen Alltag generell wichtig ist. Das gilt auch für die Schaltschränke von Rittal, die für Sto Standardkomponenten sind. Und für diese so entscheidenden Komponenten ist unsere Philosophie, dass jeder Auszubildende mindestens einmal einen Schaltschrank selbst gebaut haben muss. Denn nur so entsteht eine Vorstellung davon, was es bedeutet, zu sägen, zu bohren, Gewinde zu schneiden und zu verdrahten. Das ist aus meiner Sicht unabdingbar.“ Dieses Prinzip hat Hauschel von der Hardware konsequent auf die Software übertragen: Auch die Relevanz verlässlicher, zentral vorgehaltener Daten soll jedem Mitarbeiter bewusst sein.
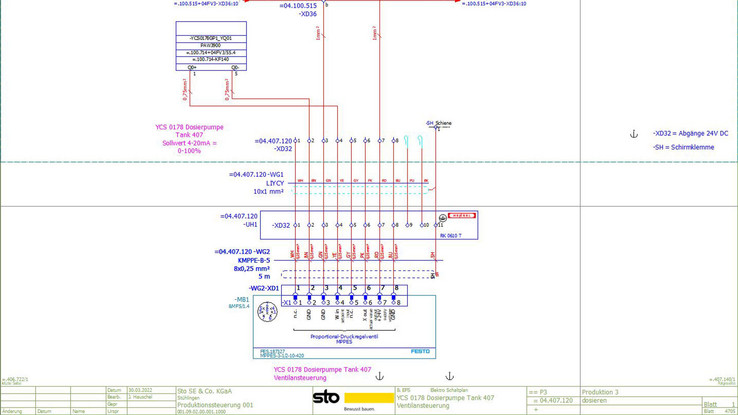
Elektrotechnische Ansteuerung von Ventilen: Die Integration der Fluidplanung in die Dokumentation der elektrotechnischen Planung mit EPLAN Fluid hat nicht nur das Engineering beschleunigt, sondern vereinfacht auch Produktion, Wartung und Instandhaltung.
© Sto
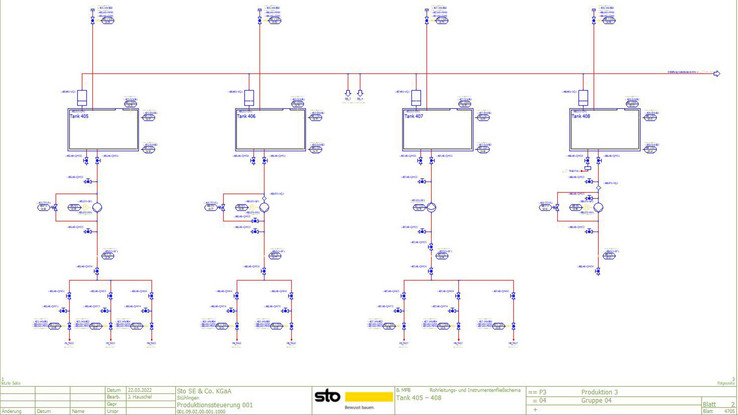
Tanks und verbundene Instrumentierung im Fließschema von EPLAN Preplanning: Werden Rezepturen geändert, muss Sto regelmäßig Umbauarbeiten vornehmen, um die Anlage entsprechend anzupassen.
© Sto
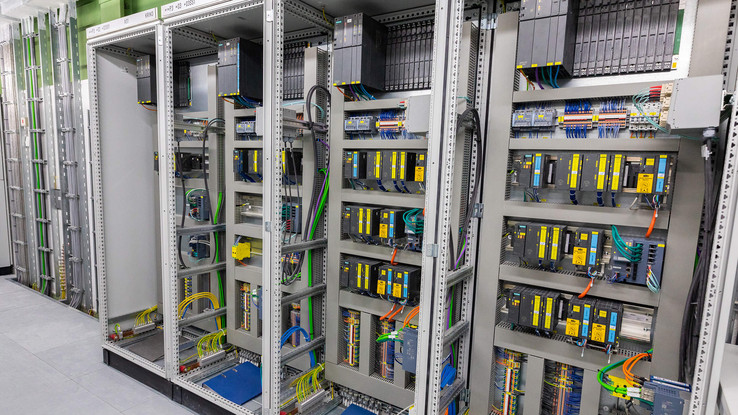
Blick in einen Schaltschrank der Anlage, die jetzt lückenlos in EPLAN erfasst ist. Vorteil des Dreigestirns aus EPLAN Preplanning, Electric P8 und Fluid ist, dass die Sto-Konstrukteure alle Pläne und Änderungen jetzt auch selbst durchführen können.
© Sto
50 Prozent Zeitersparnis im Arbeitsalltag
Für die Datenhaltung waren die Werkzeuge von EPLAN ab Projektbeginn die führende Größe. „Alle Daten, die irgendwo verarbeitet werden – ob Texte, Betriebsmittelkennzeichen oder sonstige Hinweise – werden aus EPLAN in andere Systeme exportiert, sodass alles immer synchron ist“, erklärt Hauschel die Vorgehensweise. Da Änderungen in der Verfahrenstechnik oder der Steuerung der Produktion zum Tagesgeschäft gehören, arbeitet er täglich mit den Tools: „Outlook, Teams, EPLAN – diese Programme starte ich jeden Morgen als erstes, sobald ich am Schreibtisch sitze, denn ich benötige sie während der gesamten Arbeitszeit.“
Nach dem Ergebnis der Entscheidung für den gebündelten Einsatz von Preplanning, Electric P8 und Fluid gefragt, muss der Planungs- und Automatisierungsexperte nicht lange überlegen. „Die Zeitersparnis liegt bei mindestens 50 Prozent. Schließlich mussten wir früher oft bei Problemen durch die Anlage laufen. Heute orientieren wir uns stattdessen am Fließschema und haben immer sofort den kompletten Überblick.“ Dass die Pneumatikpläne nun ins Gesamtschema integriert sind, erleichtere den Alltag zusätzlich. „Die Sprungfunktion zwischen den verschiedenen Disziplinen ist einfach schön“, freut sich Hauschel.
Effizienz im Betrieb und darüber hinaus
„Das System hat auch eine Kommunikationsbasis aufgebaut“, ergänzt Ronny Kaltschmid, und verweist damit auf Vorteile, die über die Produktion und die Sto-eigenen Mitarbeiter hinausgehen – auch Lieferanten, Instandhalter und weitere Dienstleister profitieren von der zentralen, integrierten Datenhaltung. Hauschel bestätigt das: „Die zuverlässige Datenbasis hat uns nach innen und außen effizienter gemacht. Steht etwa die Instandhaltung eines Anlagenteils an, gibt ein in EPLAN erzeugtes PDF dem Dienstleister ein viel umfassenderes Bild als es eine Liste mit den verbauten Komponenten bieten würde.“
Über 500 Stromlaufpläne umfassen die Anlagen von Sto in EPLAN Electric P8. Für drei der Produktionsanlagen in Stühlingen wurden bereits die R&Is in EPLAN Preplanning abgebildet, 50 pneumatische Schaltpläne wurden nach dem aktuellen Stand mit EPLAN Fluid eingepflegt. „Das System wächst ständig“, betont Joachim Hauschel – schließlich sind Änderungen und Erweiterungen sein Tagesgeschäft. „Und aus diesem Tagesgeschäft ist EPLAN nicht mehr wegzudenken.“
Auf einen Blick: Retrofit bei Sto mit EPLAN
- Retrofit einer Produktion mit Durchsätzen von bis zu 1.000 Tonnen pro Tag
- Abbildung der R&Is für drei Produktionsanlagen in EPLAN Preplanning
- 500+ Stromlaufpläne in EPLAN Electric P8
- Zugesicherte Anlagenverfügbarkeit von 98,5 Prozent
- >50 Prozent Zeitersparnis bei Planung und Automatisierung
Autor: Marius Schaub, freier Fachjournalist, München